WEINIG scanner systems: Recording everything at a glance
Fully-automatic, high-performance lines are being used increasingly in modern wood processing, even in rough mill applications. An upstream scanner is an integral component of the overall system. The scanner records the relevant timber data on all sides in the blink of an eye (knots etc.) and supplies this to the machines downstream, such as rip and cross-cut saws, at full production speed. Without automatic recognition systems like this, the cutting performance of the overall systems would be unimaginable. This places the highest demands on the control technology.
The WEINIG development departments provide solutions for highly automated production lines. We guarantee reliable production processes - for hardwood and softwood applications. WEINIG offers the right configuration for every application.
The SOLID SCAN Sense series sets new benchmarks in the further development of scanner technology. The innovative, completely revised product portfolio offers higher performance and significant optimization of the traditional scanner strengths. The SOLID SCAN Sense series provides solutions across all process stages: from ripping and cross-cutting applications to a range of variants for use as a sorting scanner.
The SOLID SCAN series offers efficient performance features at attractive prices and is specially designed for the requirements of smaller companies with simple cross-cutting applications. It is capable of feeding a single cross-cut saw and has the efficient and powerful optimization of the SOLID SCAN Sense series.
With EScan, the product range has been extended to strength grading. A range of different options for sorting by strength now enable certified production of glulam, DUO, TRIO and other strength-related products.
WEINIG SOLID SCAN 4000 series
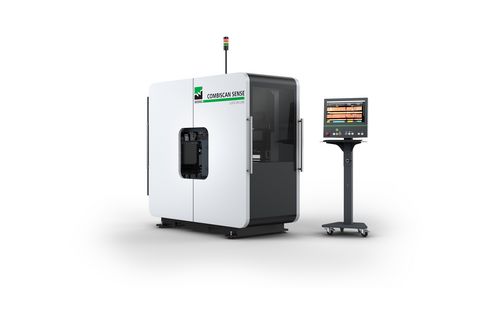
Maximum performance and flexibility
- Fast return on investment
- Optimization of your products by value, utilization or production objective
- Extensive statistical functions in real time
- Compatible with all high-performance optimizing cross-cut saws, high-performance rip saws and sorting systems
- Optional processing of random width boards in a single production run
WEINIG SOLID SCAN 2000 series
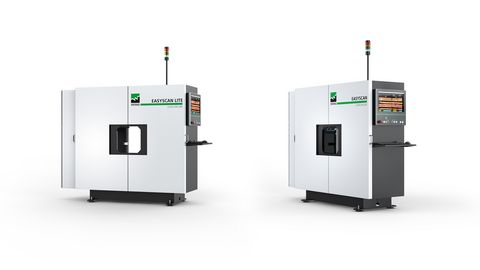
The most profitable solution for wood optimization
Detail page SOLID SCAN / SOLID SCAN LiteWEINIG SOLID SCAN T 2100 R series
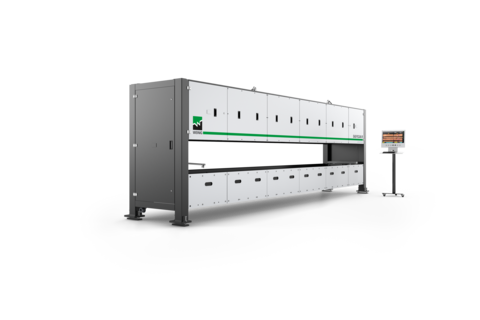
The most profitable solution for wood optimization
- High productivity thanks to automated defect detection
- Reduced labor costs, since labor-intensive manual marking is dispensed with
- Increased recovery since the detection accuracy of the scanner is far superior to manual marking
- More flexible production since many different qualities and products can be produced at the same time
- Increased quality of end products
WEINIG EScan series
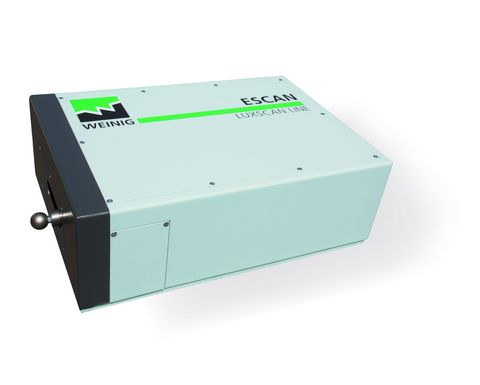
A new dimension for sorting by strength
- Up to 180 boards / minute
- Dynamic E-module measurement via laser interferometer
- Density measurement via dynamic weighing and dimension measurement
- Measurement during throughout feed (board does not have to be stopped for measurement)
- Easily integrated into existing production lines